// NEWS RELEASE
Upgrades Enhance Researchers’ Rapid Prototyping Capabilities
BIO PRINTING TECHNOLOGY ON HORIZON
CCDC Chemical Biological Center Public Affairs | November 20th, 2019
Upgrades Enhance Researchers’ Rapid Prototyping Capabilities
BIO PRINTING TECHNOLOGY ON HORIZON
DEVCOM CBC Public AffairsNovember 20th, 2019
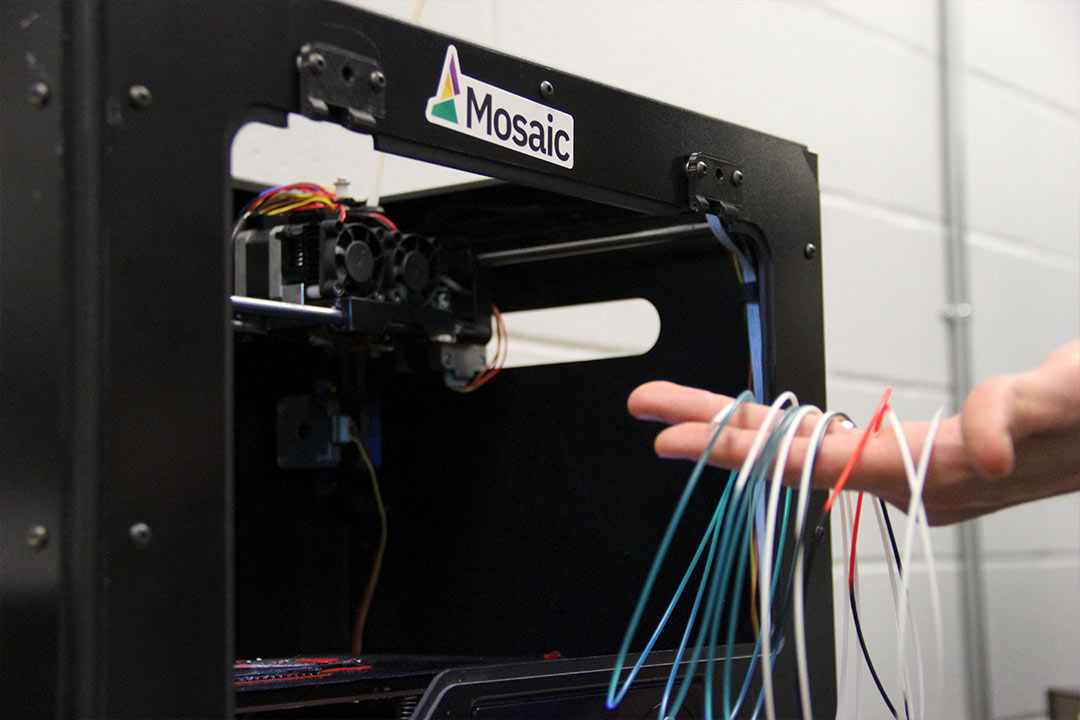
The multi-material filament system allows printing of up to four different materials at once by calculating how much material is needed for each material break per layer.
MakerSpace at the U.S. Army Combat Capabilities Development Command (CCDC) Chemical Biological Center now has new equipment to help researchers design and produce special parts for their projects.
“We’ve added the capability of running two different materials in the same build,” said Bradley Ruprecht, engineering technician. “We’ve had the capability to do that, but some new machines have come on the market that do a better job.”
Additive manufacturing has come a long way since its beginnings in the mid-1980s. Where machines once used layers of paper to build a wood-like item, they now use thermo-plastic filaments to build intricate pieces.
One of those machines has helped one research team apply for a patent for a new ion mobility spectrometry drift cell design. A drift cell separates ions based on their size to charge ratios as they drift down the known length of the drift cell towards a detector.
“We are using the machines in MakerSpace to test whether additive manufacturing is a viable method for accurately reproducing a drift cell of a preprogrammed and known length. This is important because the length of the drift tube produced by the manufacturing process will affect the performance of the detector and its overall accuracy,” said Brian Hauck, Ph. D., a contract research chemist at the CCDC Chemical Biological Center.
Besides the conductive and nonconductive varieties, other thermo-plastics now include elastomerics with ridges and soluble support materials with complicated geometry.
The use of additive manufacturing or 3D printing can help researchers speed up the prototyping process. Researchers can print parts specific to their needs early on. 3D printing also saves time because researcher don’t have to rely on another person or team to fabricate parts. It provides flexibility. If an idea for a part doesn’t work, researchers can redesign and print another iteration.
Another MakerSpace upgrade relates to machine design advances that make working with more than one material easier to accomplish.
“Some of our machines have two nozzles that deposit materials, but they are at the same height and when the process switches between them, both nozzles are hot even when it’s not in use and it has the tendency to ooze and drip material. If you have a little mixing of materials, you could have a problem,” Ruprecht said.
For the drift tube that could mean a short circuit leading to the inability guide the ions through the tube.
The new printers solve the material spill problem in three ways.
One printer has retractable nozzles on a single head, another has independent heads and the third solution is a called a multi-material filament system.
Imagine printing out a toothbrush that has a rigid handle with an area that is rubber, say for a thumb grip. The multi-material filament system will calculate how much rigid plastic is needed then connect to that the amount of rubberized material needed, so it combines two or more source filaments into one thread for each layer of the toothbrush.
For making larger items, MakerSpace will soon install a Hewlett-Packard multi-jet fusion printer that uses a nylon powder. It will be an improvement over a similar printer now in use that uses a tiny laser beam to raster each layer. The HP model uses a combination of an inkjet head and an infrared lamp to shape and harden the layers making it much faster than the current printer.
Not yet installed but on Ruprecht’s list of additions to MakerSpace is a bio printer.
“We’ve had a lot of requests for it in the last year,” he said.
Bio printing provides the ability to make a 3D ‘scaffold” out of collagen, an algaenate or some other biological material that is seeded with living cells. The cells are cultured, multiply and turn into living tissue, Ruprecht explained.
“We’ll be able to manufacture structures with living cells to mimic organs and tissue,” he said.
Producing structures that mimic human organs and tissue provides a superior research environment when investigating the effects of chemical warfare agents on people.
Once they settle on a printer and MakerSpace staff is trained, bio printing will be available for researchers.
Ruprecht admits that learning all the ins and outs of additive manufacturing might be a bit intimidating, but says the knowledge is worth mastering.
“We provide education and training. We train researchers on how to use CAD – computer aided design – so they can create their own three dimensional parts. We teach them how to use the 3D printers,” Ruprecht said. “We have had some researchers really take to it.”
For researchers not quite sure about the technology, MakerSpace personnel are there to help.
“It’s learning skills and learning processes and the materials available to augment their process, but we also consult and help point people in the right direction,” he said.
The U.S. Army Combat Capabilities Development Command (DEVCOM) leads in the discovery, development and delivery of technology-based capabilities to enable Soldiers to win our nation’s wars and come home safely. DEVCOM is a major subordinate command of the U.S. Army Futures Command. The DEVCOM Chemical Biological Center is the Army’s principal research and development center for chemical and biological defense technology, engineering and field operations. The DEVCOM Chemical Biological Center is headquartered at Aberdeen Proving Ground, Maryland.