// NEWS RELEASE
3D Printing Research Looks Beneath the Surface for Future Solutions
Research could influence protective equipment production and requirements
CCDC Chemical Biological Center Public Affairs | January 13th, 2020
3D Printing Research Looks Beneath the Surface for Future Solutions
Research could influence protective equipment production and requirements
DEVCOM CBC Public AffairsJanuary 13th, 2020
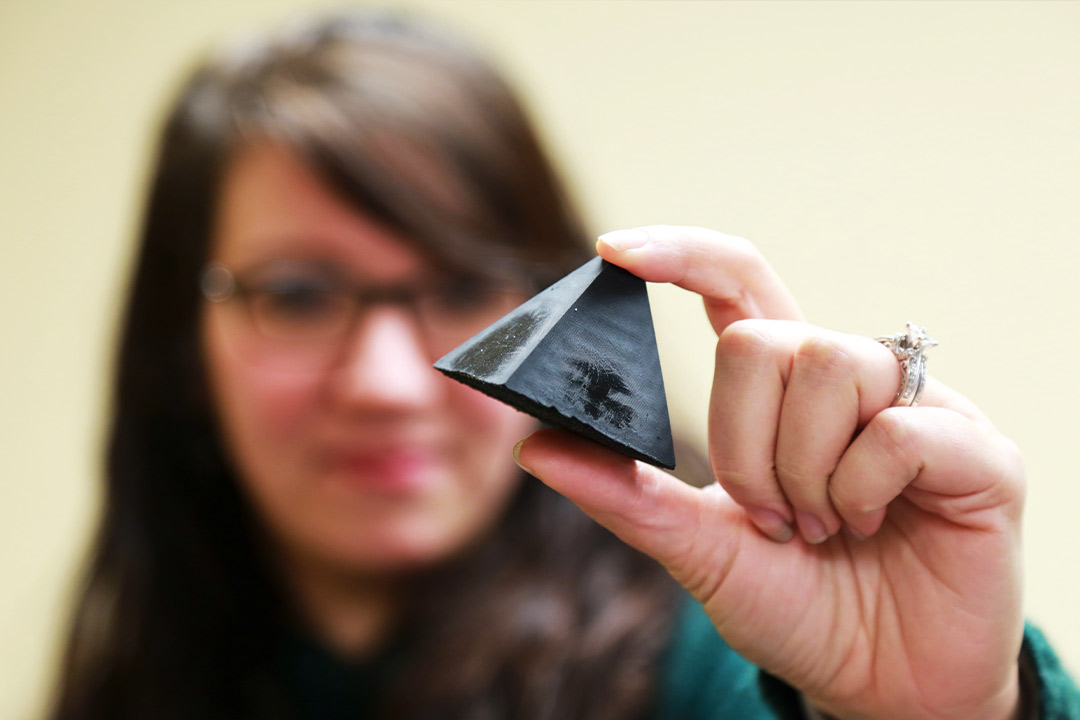
Angela Zeigler, Ph.D., holds one of the 3D printed objects being tested. Photo by Shawn Nesaw.
A gas mask is a necessity on the battlefield. Every warfighter receives one and is trained to use it. But what if it’s damaged or doesn’t fit right? Getting a new one when you’re halfway around the world could take time and negatively impact missions. In the age of 3D printing, it’s imaginable to 3D print a protective mask for a warfighter on demand. But do we know enough about 3D printers and the material they use to rely on it to keep warfighters safe from a chemical or biological agent attack?
Jerry Cabalo, Ph.D., and Angela Zeigler, Ph.D., researchers at the U.S. Army Combat Capabilities Development Command (CCDC) Chemical Biological Center, would argue no, which is why they have embarked on a new study that looks beneath the seemingly solid structure of 3D printed objects to identify pores and voids that would allow harmful materials to pass through the object.
“We don’t really understand 3D printed material very well,” Angela Zeigler, Ph.D., said. “We’re interested in understanding how a chemical diffuses through a 3D printed material. We developed a Surface Science Initiative (SSI) plan to better understand 3D material and the pores and voids in a material.”
Technological advances in the past 20 years have allowed the U.S. Army and other branches of the military to leverage emerging technology for the good of the warfighter and 3D printing is one such technology. While 3D printing, a form of additive manufacturing, might not feel “emerging” these days, with the pace of new technology quickening every day, the techniques, materials and possibilities are still fairly untapped.
Cabalo and Zeigler worked with the Center’s Additive Manufacturing facility to 3D print hundreds of 1-inch by 1-inch square chips of different 3D printing materials and of different thicknesses. Once all the chips were printed, they began data collection.
To understand the porosity of 3D printed materials, chips of different thicknesses and materials are printed and then tested.
“We’re looking to map out the space throughout a seemingly solid 3D printed object,” said Zeigler. “In doing so, we’ll be able to determine the diffusion threshold of each material.”
Beyond that, they would like to understand the fundamental process of molecular diffusion through porous material. This knowledge will potentially give the Army the capability to use 3D printing to develop warfighter personal protective equipment. A combination of computational modeling and experimentation will further the understanding of how porosity affects the movement of toxic chemicals.
It turns out, those 3D printed objects, while they may appear solid, actually contain lots of hollow space. If researchers are to one day 3D print gas masks, they’re going to need a printer and a material that can print materials with little to no voids which allow chemicals to permeate.
The research consists of laboratory data and modeling data. The laboratory data is collected by Mark Varady, Ph.D., and Melissa Hulet, researchers at the Center, using a vapor testing method where each 1x1inch 3D printed chip is sandwiched between two silicone blocks. On one side, a given vapor passes through the 3D printed material and on the other side dry nitrogen is sweeping across the material, capturing any vapor that breaks through the material. That information is sent to a mass spectrometer that detects whether any vapor diffused and how much made it through the material.
3D printed materials, both the chips and a few more complex 3D structures, are sent to the CCDC Army Research Laboratory where they are processed using a new technique called micro CT, similar to a large x-ray scan. The micro CT scans provide one representation of the pores and voids of 3D printed material. Zeigler and Cabalo are able to quantify the data and visually represent the voids in the 3D printed material, inching closer to a better understanding.
Taking the research, a step further, the team partnered with Roseanna Zia, assistant professor of chemical engineering at Stanford University, who specializes in colloidal dispersion and diffusion modeling. As experts in the field of diffusion modeling, Zia and her team are creating dynamic models to realistically simulate the diffusion of chemicals through the 3D printed material based on the data Ziegler and Cabalo provided.
“The data is great but having models that show diffusion through a 3D printed material makes the data really work for us,” Cabalo said. “Once we have a model that properly predicts what happens, we can dig in deeper to see how porosity controls permeation. The models are also more visual, so they help us communicate our findings to a wider audience.”
The team is still in the throes of research — printing, testing and gathering more data and developing more models that will lead to the comprehensive toolkit they envision.
The red particles shown at the top of the graphic are solvent tracer particles. During the simulation, the particles are tracked as they move through the pore network (3D printed material) to arrive at the opposite of the simulation box. (Image provided by Stanford University.
While 3D printing is currently used in the field, it’s not used to print protective masks and suits and the printers and material are fairly standard. In the future however, as the Army looks to home in on the best printers and best material for specific functions, like augmenting collective protection efforts, this fundamental testing could end up impacting requirements and military doctrine related to 3D printers and printer material.
“When you look at the complexity of 3D printing, there are so many variations. Having a set standard for creating protective equipment is necessary,” Zeigler said. “We hope our research influences future decisions.”
As rapid prototyping and development remains a focus area for the Army, more fundamental research like this will be important to ensure an in-depth understanding is captured before making bigger decisions that impact the warfighter.
“It’s our duty to ensure warfighters are prepared to combat chemical, biological, radiological and nuclear threats during missions,” Zeigler said. “We’re always thinking of the next quick, low cost solution that lessens the weight burden but increases warfighter effectiveness. 3D printing certainly has its benefits, so we want to ensure it provides a reliable, effective solution.”
The U.S. Army Combat Capabilities Development Command (DEVCOM) leads in the discovery, development and delivery of technology-based capabilities to enable Soldiers to win our nation’s wars and come home safely. DEVCOM is a major subordinate command of the U.S. Army Futures Command. The DEVCOM Chemical Biological Center is the Army’s principal research and development center for chemical and biological defense technology, engineering and field operations. The DEVCOM Chemical Biological Center is headquartered at Aberdeen Proving Ground, Maryland.